Process Optimisation in Production using AI
When one talks of introducing artificial intelligence to the metallurgical industry, the idea might seem baffling yet novel, but certainly not impossible. Metallurgical production encompasses several complex and scattered operations, from preparing raw materials to manufacturing the final metal production.
In metal production, ongoing maintenance of equipment and production machinery incur high costs, where unplanned downtime costs an estimated $50 billion per year globally, and asset failures are the cause of 42% of downtime.
Several forward-thinking manufacturers adopt predictive and prescriptive analytics tools to predict equipment and process breakdown and prescribe process parameters to mitigate errors, save substantial costs and time. Adopting this method of data analysis to existing production methods can be done with the right planning and research. If you are looking to employ predictive and prescriptive analyses in your production plant, here’s what you need to know.
Digitizing the foundry industry via an AI-based solution
The lack of efficiency over the entire manufacturing value chain fuels the adoption of AI-led soft computing architectures. Gaining a holistic view of the whole value chain and optimizing every process for efficiency can be challenging. However, by leveraging artificial intelligence, the foundry industry can gain enhanced profits and sustainability in the future.
The global metal industry is going through rapid digitalization now more than ever, and there is an urgent need to address the existing production challenges. Despite the adoption of cutting-edge technologies like IoT, cloud computing, and machine learning, several factors still challenge production at scale.
Predictive and Prescriptive Quality, Energy, Maintenance, and Production Planning are new technologies that enable plants and foundries to achieve such a goal, through the optimization of quality efficiency and indirect savings through better scheduling, effective use of human resource, and sustainable utilization of raw material.
Here comes the catch, such benefits call for future-driven and cost-effective service providers who possess domain knowledge and can complete the metallurgical puzzle with their self-reliant AI models, domain knowledge, and seamless integration and optimization procedures. And that’s precisely what Tvarit- the Industrial AI Solutions start-up offers. A viable metallurgical architecture for today and for the future.
Data is a key enabler of AI and a goldmine for the metal-working industry, a treasure trove waiting patiently to be explored and analyzed. To make accurate predictions to gain insight and prescribe corrective measures to avoid errors, there should be a robust set of data to guide the model.
But, how do we extract the data from this “goldmine” of machines, sensors, quality systems, MES, and ERPs?
Tvarit’s Industrial AI solutions are designed to collect existing information from production equipment and predict breakdowns, errors, and scrap waste production even before they occur. It applies prescriptive maintenance models to develop specialized recommendations and corrective actions to reduce downtime and increase availability. Our software is fortified by Amazon AWS technologies. All relevant production data is securely stored in Amazon’s AWS Cloud, offering a cost-effective and scalable solution for data storage and processing, ensuring that your AI-driven production optimization is both powerful and efficient.
Furthermore, Tvarit also applies Prescriptive Quality to recommend optimal process parameters to rectify unfavourable quality deviations, Prescriptive Energy to reduce high energy consumption, and Prescriptive Production Planning to optimize production flow.
But to harness the prescriptive models, manufacturers need to be AI-ready. This is how we get there:

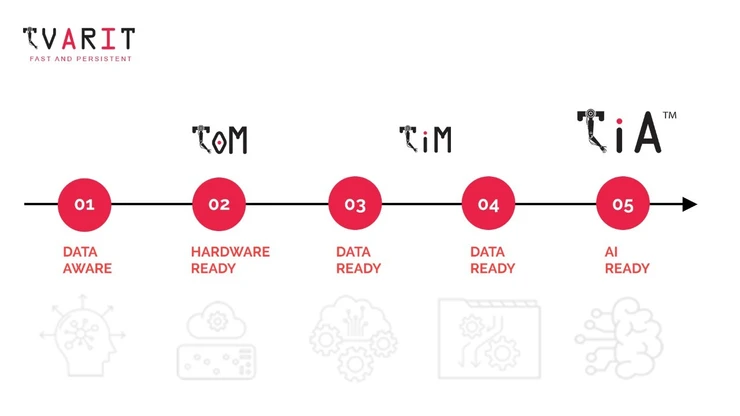
The steps to an AI-championed production journey: TOM, TIM, and TIA
TOM (Tvarit Observant Module):
The Tvarit Observant Module invokes this observant power by monitoring machines and operations in real-time to ensure accurate digitization of production processes and provide transparency for better decision-making.
TOM is considered the first step towards digitalizing the production data that enables manufacturers to monitor equipment and processes in real-time. It can:
- Identify the potential for increasing machine availability and overall system effectiveness
- Gain insight into the production and recognize anomalies
- Get non-invasive extraction of machine and process data in real-time
- Find causes of errors and failures
TIM (Tvarit Intelligent Monitoring):
Tvarit Intelligent Monitoring builds a personalized end-to-end digitized enterprise solution that places all your machines and processes under one roof- a centralized monitoring software. Moreover, it also enables 360-degree real-time monitoring of your entire production cycle to elevate profit margin, reduce scrap output, and improve machine availability.
TIM connects all the equipment, digitalizes the production, and optimizes the processes. To be more precise, TIM offers a complete smart factory solution and connects the machines and processes in a central condition monitoring software. It then provides comprehensive and valuable insights into the production processes and key figures. Based on this, manufacturers can make more informed and better decisions and increase efficiency and profitability.
Key features of TIM:
- Comprehensive OEE & fundamental figure analysis
- Complete process monitoring
- Failure and malfunction analysis
- Resource Management
With this solution, enterprises can:
- Identify bottlenecks and devise actions to process optimization.
- Analyse factors that contribute to machine inefficiencies
- Gain a complete view of production cycles.
- Get insights on how to improve OEE, reduce waste, boost resource efficiency, and optimize production costs.
- Identify, monitor, and track KPIs.
TIA (Tvarit Industrial Artificial Intelligence):
Tvarit Industrial Artificial Intelligence software is a ready-to-use state-of-the-art smart factory and digital software based on machine learning. TIA employs the power of AI to prepare dynamic software comprising predictive and prescriptive quality, energy, planning, and maintenance. From digging deep into raw data to optimize processes in the present and suggesting actions for the future, TIA functions as a valuable asset for your business.
Even better, TIA also engages in:
- Predicting breakdowns, product quality, energy consumption and process efficiency.
- Offering recommendations to gain optimal product quality, energy efficiency, environmental sustainability, and maximum machine availability
- Preventing product deviations, machine failures, and breakages beforehand
Key benefits for manufacturers and enterprises:
- 100% transparency of the data
- Predictive analytics
- Prescriptive recommendations for process optimization
- 360° real-time monitoring
- Tools for intra and cross-departmental collaboration
Reimaging production with Tvarit’s AI journey
With resource scarcity, high production costs, and growing environmental concerns, the foundry, and metal production industry must do things differently to sustain, survive and thrive. Together with Tvarit, manufacturers can derive a pragmatic view of an enterprise AI ecosystem, one that ensures success at every step.
If you want to stay up to date on this topic, follow us on LinkedIn or feel free to contact us here.